The Power of Powder
A Glimpse into Additive Manufacturing
Susie Henaghan
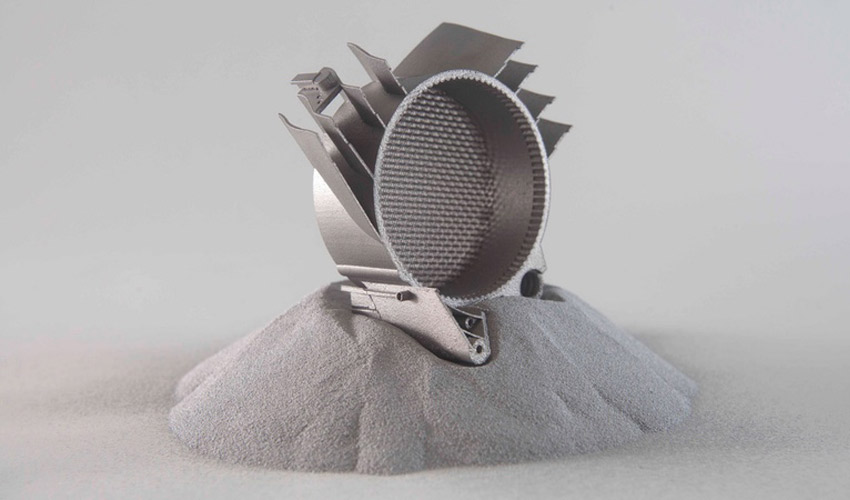
Since the dawn of the Bronze Age, manufacturers have been on the search for cutting-edge technologies that would greatly reduce cost, production time and resources.
Better, faster, cheaper.
Traditional methods, while tried and true, have been costly and complex. With the introduction of 3D printing, additive manufacturing has been shaping the future of our world—quite literally!
But what is additive manufacturing? And how will it help you?
Join us as we examine the many layers of additive manufacturing:
Additive manufacturing, more commonly known as 3D printing, is a process which creates a physical object from a digitally created design. Computer-aided design (or CAD software) maps out a product and documents the entire design process. CAD facilitates the manufacturing process by transferring detailed diagrams of a product’s materials, processes, tolerances and dimensions with specific conventions for the product in question.
The 3D design is then digitally “sliced” into superfine layers as the product will be formed layer by layer, then uploaded to an additive manufacturing machine.
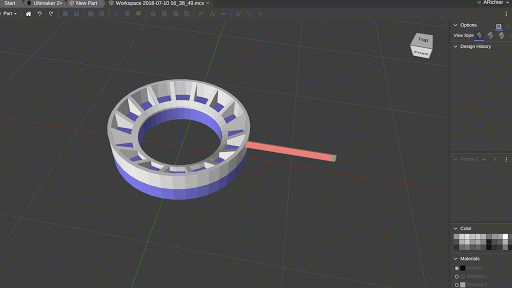
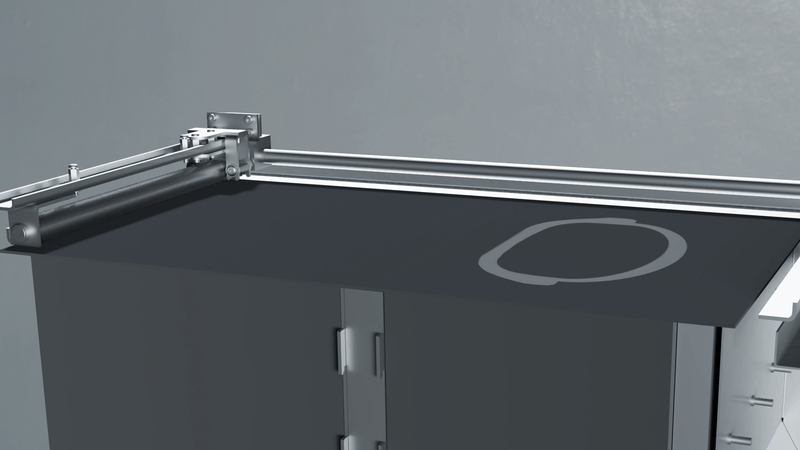
Manufacturing begins with a thin layer of powder spread evenly across the design platform. Next, a heat source, such as laser or electron beam, melts the first layer. The platform is then lowered while another layer of powder is then evenly distributed, as the process repeats again following the mapped design. Each successive layer bonds to the preceding layer of melted or partially melted material.
The excess powder is then removed and will be used again in another process (thus reducing waste) and the newly created object is revealed.
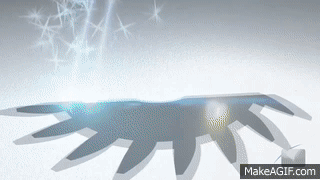
Additive manufacturing allows you to produce parts that are lighter, stronger, and more durable than traditionally made parts, while reducing build time. This has also given rise to a unique micro-structure and mechanical behavior which has been unattainable with traditional manufacturing. Also, additive manufacturing adds precise features and complex geometries that were seemingly unavailable with traditional manufacturing. The journey from a design file to functioning design is revolutionizing manufacturing.
The benefits of additive manufacturing (AM) is multi-faceted as the designs it can create. From cost reduction to design customization, we’ve broken down some of the amazing benefits it brings to the table:
A key benefit offered is the ability to achieve intricate geometries and small organic features that have been extremely difficult or impossible to produce with traditional manufacturing approaches. For instance, GE Aviation saw an issue with their fuel nozzle tip production. The interior geometry was too complex and was comprised of 20 individual pieces manufactured by traditional methods, which were then welded and brazed together. By switching to additive manufacturing, GE was able to produce the fuel nozzle tip as a complete, singular part in a fraction of the time and without the waste generated by individual sub-assembled pieces.
The benefits exceeded far past the fact it was now one solid piece, as the simpler design weighed 25% less than the original nozzle yet was five times more durable. It also improved fuel burn by 20% and achieved 10% more power. In aviation, design complexity meant added expenses—but now additive manufacturing reduces cost and increases efficiency and offers design freedom that designers could never experience before.
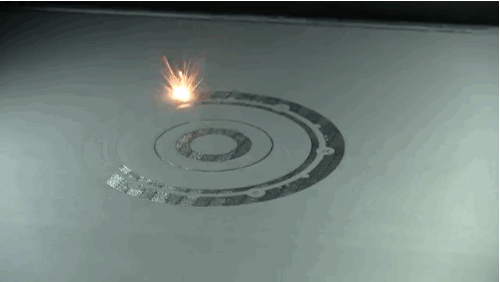
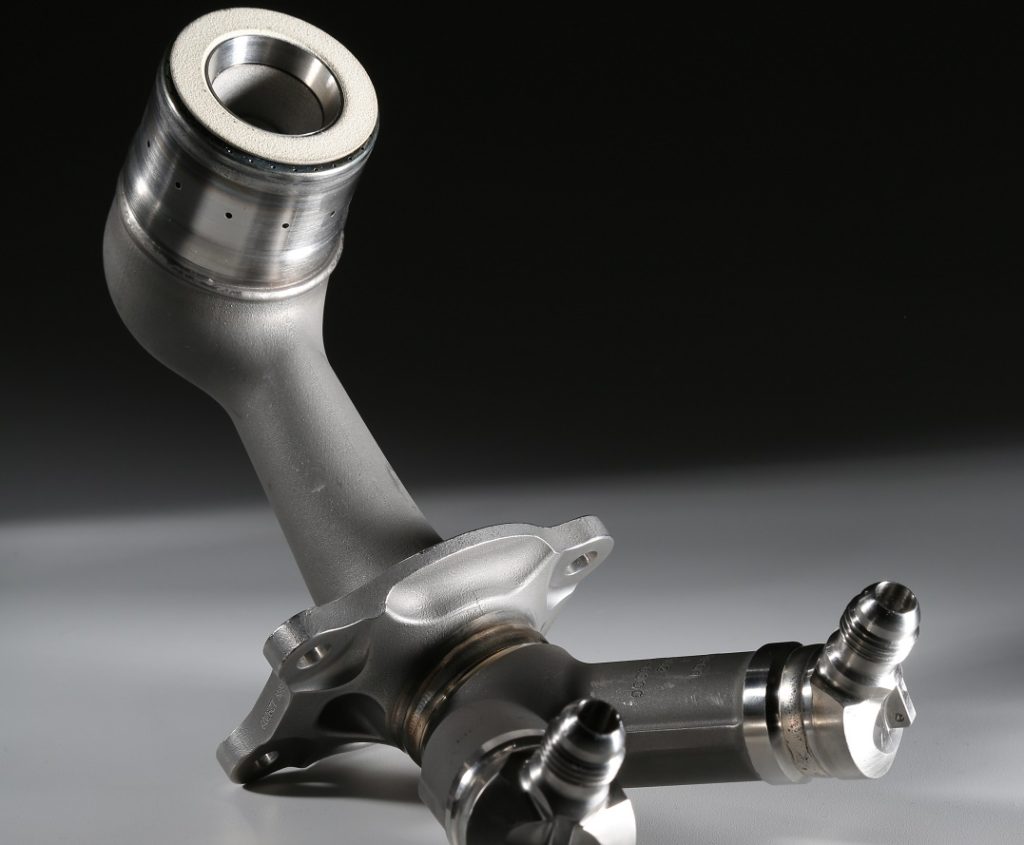
GE’s fuel tip nozzle created with additive manufacturing
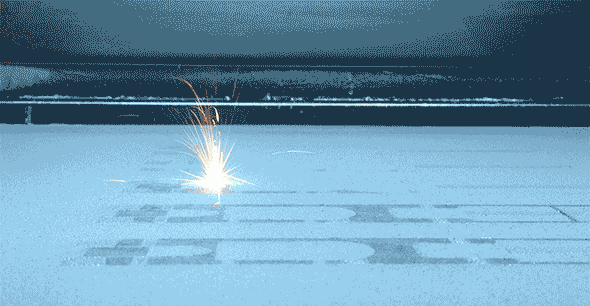
With traditional manufacturing, multiple parts are designed separately, manufactured then transferred to be assembled to form in a multitude of lengthy time-consuming processes that will take weeks to months to complete. The streamline process of additive manufacturing allows for a speedier process, thus decreasing previous overwhelming lead times.
Theoretically, a product can be designed, printed and tested on the same day which eradicates several stages in what used to be lengthy product development process. The speed aids to designers to print several prototypes which allows quick verification before committing to a full-scale production. Also— multiple of products can be simultaneously created in one batch printing compared to traditional manufacturing’s one-at-a-time approach.
Traditional manufacturing is a subtractive method of production—cutting away until the final product is produced leads to a considerable amount of leftover waste. While it can be recycled, this requires excess labor and becomes time-consuming as many processes are put into place to get the metal back to working form. Additive manufacturing is called so as it adds material to the part rather then cut away. With additive manufacturing, any excess metal powder is then collected in excess bins for re-use in the next production cycle, so there is little to no waste.
Also, chemical and toxic fumes that are created during traditional manufacturing are practically removed with 3D printing. While the AM machines have a high energy consumption—it still isn’t as high as traditional injection molding. Additive manufacturing is also lending a hand at reducing its carbon footprint, especially in the aerospace sector.
Remember that fuel nozzle we discussed that reduced it’s weight by 25%? With more lightweight material being used in constructing airplanes, the less carbon emissions will be emitted. Every 5.5 lbs of weight on a plane equates to 1 ton of carbon emissions per year.
These little changes are what will make a bigger difference in the long run!
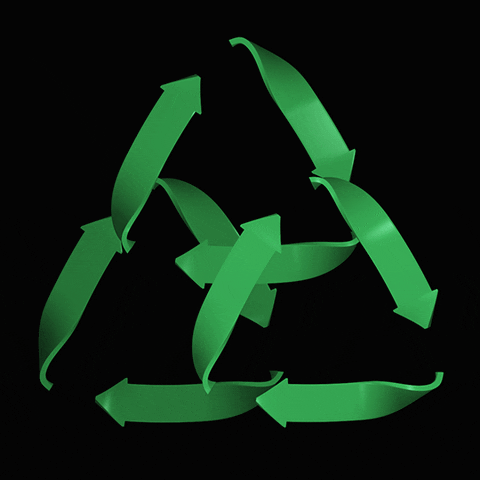
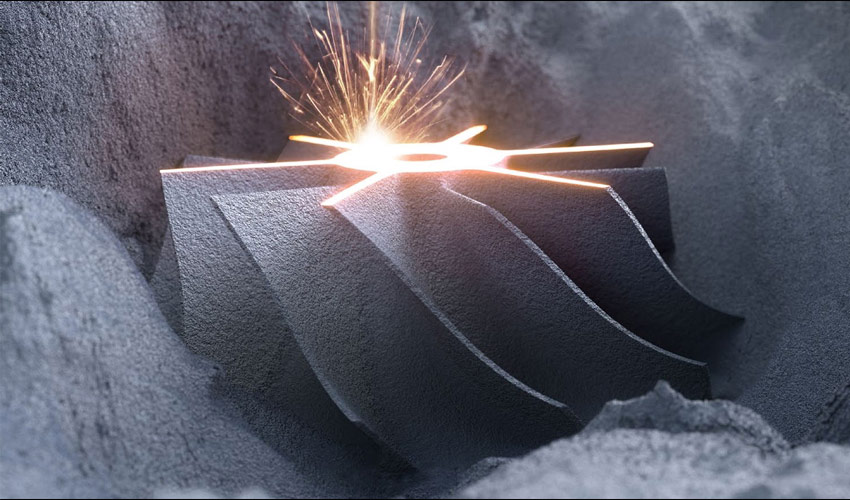
While traditional manufacturing is an important crux of the industry—it’s easy to see why additive manufacturing is designing an efficient and effective future.