Magnificent Magnesium
Making the Most of this Mineral
Susie Henaghan
Lightweight. Low-density. High corrosion-resistance. It’s easy to see why magnesium alloys are so sought-after in engineering applications as they provide properties that are critical to expert designing. Magnesium alloys are also known for their strength, good heat dissipation, and good damping. The properties of magnesium alloys makes them easy to weld, forge, cast or machine.
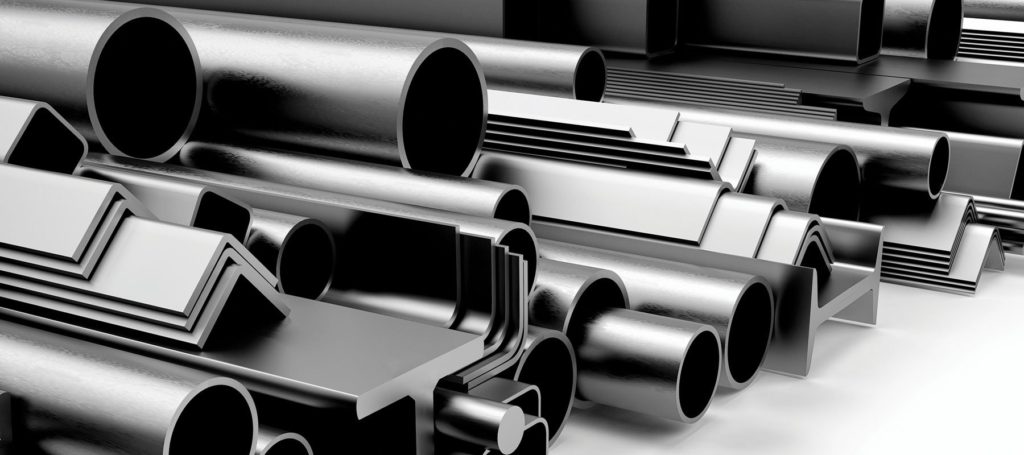
Let’s Extract Some More From This Ore…
By alloying with other metals, the benefits of magnesium alloys only increase. Magnesium alloys are the third most popular non-ferrous casting material. The physical properties of the alloys change based on their chemical compositions. Adding different alloying elements will result in different properties under different conditions.
- Aluminum improves strength, hardness, and ductility
- Zinc increases room-temperature strength, fluidity in casting, and corrosion resistance
- Manganese increases the resistance of Aluminum-Manganese and Aluminum-Zinc-Manganese alloys to saltwater corrosion by forming intermetallic compounds with iron-like metals, which will be removed during melting
- Rare earth metals help increase strength and resistance to high-temperature creep and corrosion and decrease porosity and weld cracking
- Zirconium is a strong grain refiner when added to alloys containing zinc and rare earth metals
- Beryllium helps decrease surface oxidation during casting and welding
- Calcium increases grain refinement, which helps in controlling the metallurgy of the alloy
Planes, Trains, and Automobiles…
Magnesium alloy development traditionally has been piloted by the aerospace industry to fulfill the need for lighter-weight materials that can operate under exponentially demanding conditions. One of the biggest benefits of magnesium alloys is its low density, which is only two-thirds that of aluminum. Newer magnesium alloys have yielded superior corrosion performance, which has also been a major component in the widespread use of magnesium alloy castings and wrought products.
With advancements of high-speed trains, magnesium alloys could produce railway vehicles with less weight, and aid to the reduction of noise and vibration.
Improvements in mechanical properties and corrosion resistance have led to investments in magnesium alloys within the car industry. This February, at the Battery Electric Vehicle Architectures (BEVA) in Detroit, Galaxy Trade & Technology has introduced ground-breaking strategies for making electric vehicles more efficient with the use of magnesium alloys.
“We’re pleased to report the conclusions of our preliminary joint study to industry leaders: correct application of magnesium alloys can make vehicles up to 25% lighter. This study answers one of the most urgent needs of the fast-growing electric vehicle industry: increasing the distance that vehicles can go before they need to be recharged,” said Michael North, chairman of Galaxy. “The magnesium advantage can extend the typical range substantially, in one simple, fast and economical step.”
Magnesium alloys have also made significant advances within the biomedical industry. Not only is the element naturally occurring in the body, but magnesium alloys also have proven biocompatibility—proving them safe for orthopedic implants. Furthermore, magnesium promotes new bone growth, and it does not take on water, which would cause a loss in its integral shape during degradation.
Alloys International is an AS9100D worldwide distributor and specialty producer of magnesium grades such as AZ31, AZ61, AZ80, AZ91, ZK60, HK31, HM21, ZE41, ZC71, ZM21 and AM40 among others.
We supply many forms in both wrought and cast magnesium alloy.
Give us a call today to learn more!