Stainless Steel 330
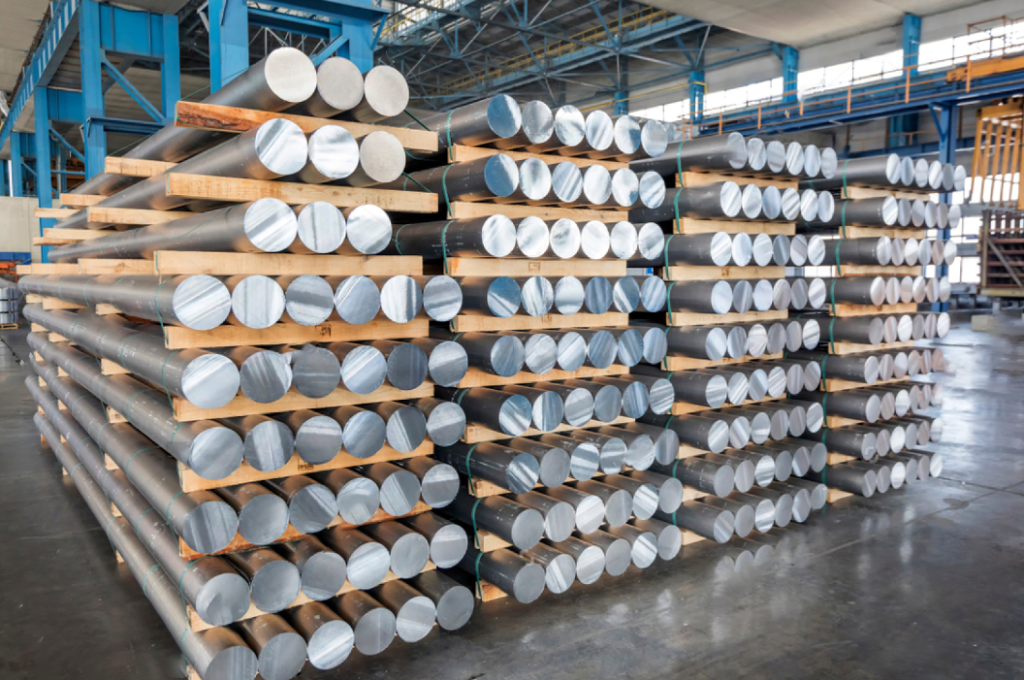
Material Data Sheet
330 steel is an austenitic heat and corrosion resisting alloy that offers a combination of strength and resistance to carburization, oxidation, and thermal shock. 330 stainless steel was designed for applications in high-temperature industrial environments where good resistance to the combined effects of carburization and thermal cycling is required, such as the heat treat industry. Carburization and oxidation resistance to about 2100°F are enhanced by the silicon content of the alloy. 330 stainless remains fully austenitic at all temperatures and is not subject to embrittlement from sigma formation. It has a solid solution composition and is not hardenable by heat treatment. The alloy’s strength and oxidation resistance at high temperatures make it a useful material for industrial heating furnaces.1.
Element | Content (%) |
---|---|
Iron, Fe | 42.0 |
Nickel, Ni | 36.0 |
Chromium, Cr | 19.0 |
Manganese, Mn | 2.0 |
Silicon, Si | 1.13 |
Carbon, C | 0.08 |
Phosphorous, P | 0.04 |
Sulfur, S | 0.03 |
Porperty | Metric | Imperial |
---|---|---|
Density | 8 g/cm³ | 0.289 lb/in³ |
Melting Point | 1400 – 1425 °C | 2550 – 2597 °F |
Property | Metric | Imperial |
---|---|---|
Hardness, Brinell | 139 | 139 |
Hardness, Knoop | 155 | 155 |
Hardness, Rockwell B | 80 | 80 |
Hardness, Vickers | 153 | 153 |
Tensile Strength, Ultimate | 585 MPa | 84800 psi |
Tensile Strength, Yield | 290 MPa | 42100 psi |
Elongation at Break | 45% | 45% |
Modulus of Elasticity | 550 MPa | 79800 psi |
Poisson’s Ratio | 0.27 – 0.30 | 0.27 – 0.30 |

Stainless Steel 330 is used in the following application areas:
- Furnace containers-carburizing, carbonitriding, annealing malleablizing
- Muffles, retorts
- Bar frame heat-treating baskets
- Quenching fixtures
- Radiant tubes
- Salt pots
- Furnace fans and shafts
- Conveyors
- Tube hangers for crude oil heaters adn steam boilers
- Heat exchangers
- Flares